ABC Analysis in Inventory Management: Best Practices and how to do it?
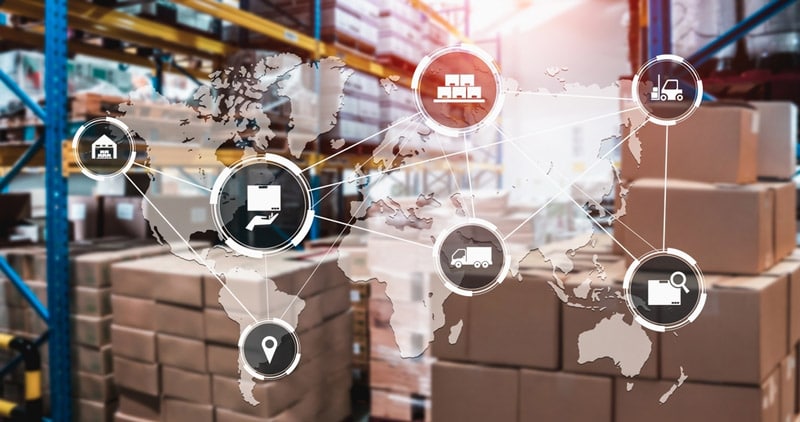
ABC analysis is one of the common and effective methods that are used in inventory management, through which the value of inventory items is determined based on the importance of each item. It is one of the important ways in any organization or company to classify its stock and determine its value. In this article, we will show you all the details about ABC analysis, what its importance is and why we use it. We will also show the most common practices using ABC analysis.
Performing an ABC analysis
The ABC analysis method is derived from the Pareto principle, and it means the method that enables the classification of companies’ stocks of goods and raw materials,
Then arrange them according to the impact they have in terms of the cost of storing them, and determine their importance accordingly.
And through the method of ABC analysis, as we have indicated, the products are classified into three categories, where:
- Category A: High value goods, including 20% of stock products that generate 80% of total revenue, and this category is of great interest to the company.
- Category B: Medium value merchandise, comprises 30% of products in stock, generates 15% of revenue, and receives medium business interest.
- Category C: Low value goods, representing 50% of the stored products, and generating returns of not less than 5% of total revenue, and the company attaches less importance than the previous categories.
What is ABC Analysis in Inventory Management?
ABC Analysis in Inventory Management determines the value of items in inventory according to the importance of each item, and is classified specifically when there are orders, whereby inventory managers collect all items in specific categories according to previous criteria.
ABC analysis helps companies and organizations understand which products or components are the most successful and which are most important at the same time, and that will contribute to the success of the company’s or organization’s financial system.
According to ABC analysis, the most important categories are A, followed by B, and the least important ones. This is what we talked about in the definition of ABC analysis in the previous part.
Why Use ABC Analysis?
You may be wondering, why use ABC analysis, but in fact this method helps to better control your inventory and helps in managing capital costs effectively, which enhances the inventory turnover rate.
The following are the most important benefits that can accrue to you from using the ABC analysis method:
1. Inventory optimization further
This is done by analyzing the products that the company needs, and thus using the spaces in the warehouses as required to store the goods in them.
2. Improved Inventory Forecasting
Through ABC analysis, it is possible to easily monitor and collect data about products that require a large demand from customers, and this will lead to more accurate sales forecasting.
3. Improve profitability
ABC analysis contributes to a reasonable increase in sales, by increasing the demand for a particular item, and all this will improve the company’s profitability significantly.
4. Strategic resource allocation
Your resources can be continually evaluated through the use of ABC analysis, thus ensuring that Class A items match the customer’s demand.
5. Provide better customer service
ABC analysis helps identify the most profitable elements for your company and then provide better levels of service for those elements, all of which will clearly contribute to customer satisfaction.
6. Better product lifecycle management
Properly predicting demand and stock levels through ABC analysis will help you better manage the life cycle of your products.
7. Control of high cost items
ABC analysis helps you prioritize demand control and maintain good stock levels, so there is always enough product available.
8. Improve inventory turnover
ABC analysis maintains inventory turnover at appropriate levels through inventory control and data collection.
9. Reduce inventory costs
ABC analysis gives you the right percentage of inventory based on A, B or C classes, so you can reduce inventory moving costs.
10. Simplify supply chain management
ABC analysis of inventory data enables you to determine when to consolidate suppliers or switch to just one supplier to reduce costs and streamline operations.
How is ABC analysis done?
As for the way ABC analysis works, it generally begins with identifying the goal that your company is trying to reach, and then collects the necessary information for classification.
After classification is appropriate, decisions are made according to that data, and the following are the steps of the ABC analysis:
- Determine the goal, and either reduce purchasing costs or increase your cash flow, by improving inventory levels according to your production or sales ratios.
- Data collection, in which it is explained collecting all the data you need regarding the determination of the total and weighted cost and the gross profit margin.
- Sorting the data, after collecting the data, the ABC analysis formula is used to arrange the demand for inventory according to cost, in descending order.
- Calculate the effect of sales. In this step, the effect of sales is calculated for each item in the inventory as a percentage.
- Sort items into purchase categories, in this step, your items are sorted after selecting the different categories. This step is important because it can help you ensure more A-class items are available in your inventory.
- Categories of Analysis after completing the previous steps of defining categories and managing costs, a number of reviews are scheduled that will help you determine the success or failure of the decisions made.
How to Implement ABC Inventory Management challenges
In order to know what is the best way to implement ABC inventory management you will first need to check whether the ABC analysis will be appropriate for your business.
LOGSTIAT Advanced Inventory Management Systems can help you with this, as it has a powerful and efficient Inventory Management System which can help you in:
- Managing multiple shelving and storage locations.
- Set and change product locations.
- Print the list of pick-up, preparation, packaging and then deportation to the shipping companies.
- View all requests received from all channels
- Create, view, search and edit orders.
- Returns management.
- Track orders (and associated inventory) and shipping.
- Inform the customer about shipping updates directly.
- View and manage customer information.
Common practices based on ABC analysis
best practices emphasize consistency, sales, and attention to events that may affect inventory levels or value.
Using technology to manage inventory is a best practice that simplifies the process from start to finish, the following are the common practices based on ABC analysis
1. Simplify categories
The simplicity of categorizing items makes them easy to move, and you can follow the method of placing the most expensive items in Class A, the average price in Class B and the least expensive in Class C.
2. Set work and service levels at the same time
It is one of the most common practices that will help you assign service levels based on the item category itself, this will ensure a more regular cycle count of critical items first.
3. Segmentation of KPIs by Category
Another important and common practice in ABC analysis is to try to create distinct KPIs, and create reports and dashboards that match each of your categories.
4. Create performance reviews
You can also use performance reviews when performing complete inventory maintenance, it is one of the effective and common practices of ABC analysis.
5. Inventory when moving
In the event that your inventory moves between locations, keep track of the time that elapsed between the date of shipment and the date of receipt, this will help you to obtain accurate inventory records that ensure that damage or loss is recorded.
6. Purposeful reclassification
Another common practice in this analysis is flexibility in classifying items, as sometimes you will need to reclassify inventory periodically due to market changes.
7. Leverage the technology and the data generated
Try to use the data to manage lead times and plan the demand, it is the most important and also successful practice in ABC analysis
Using ABC Analysis for Cycle Counting
can be used to calculate the cycle, especially since this type of analysis guarantees a larger number of important items of high volume.
Cycle counting also provides several controls that ensure accurate inventory records in the inventory management system itself.
It is also possible through ABC analysis to schedule regular cycle counting through classification.
And this will provide you with a more regular cycle counting for the items of category A, which have the greatest and most important impact on sales performance than other categories